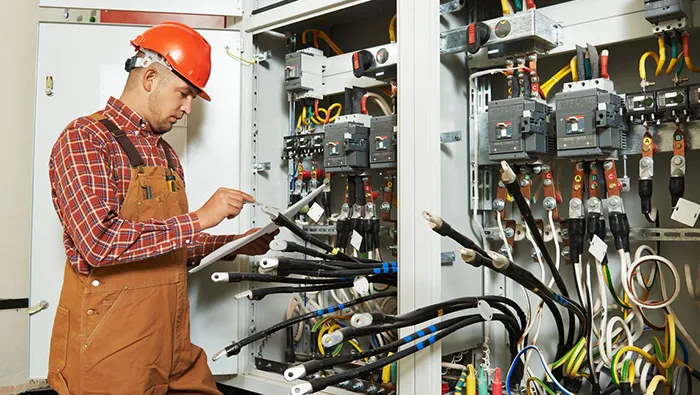
Introduction
In the realm of engineering simulations, finite element analysis (FEA) plays a pivotal role in ensuring the safety and performance of structures under various conditions. Among the most powerful FEA tools available today is Nastran (NASA Structural Analysis), widely recognized for its capabilities in performing complex structural analyses. One of the notable configurations within Nastran is Solution 146, particularly focused on MONPNT1 RMS. This article delves into the intricacies of Nastran Solution 146 MONPNT1 RMS, its functionalities, applications, and best practices for optimal results.
Understanding nastran solution 146 monpnt1 rms
Nastran is a software developed for structural analysis, originally funded by NASA in the 1960s. Over the years, it has evolved into a robust tool used across various industries, including aerospace, automotive, civil engineering, and manufacturing. Nastran facilitates the modeling of physical systems to analyze how they respond to different forces, providing engineers with insights that are crucial for design and safety.
The Significance of Nastran in Engineering
- Versatility: Nastran can handle a wide range of analyses, including linear static, nonlinear static, dynamic, heat transfer, and fluid dynamics.
- Robust Output: The software generates detailed results that aid engineers in understanding the behavior of structures under different loading conditions.
- Industry Standard: Nastran is recognized as an industry standard in FEA, making it a go-to choice for many engineers and researchers.
An Overview of Solution 146
Nastran solution 146 monpnt1 rms is a specialized analysis type within Nastran focused on modal analysis. Modal analysis is critical in understanding the natural frequencies and mode shapes of a structure, which are essential for evaluating its dynamic response.
Key Features of Solution 146
- Dynamic Analysis: Solution 146 is designed to handle the complexities of dynamic loading, helping engineers predict how structures will react over time.
- Vibration Analysis: It focuses on identifying potential resonance issues by calculating natural frequencies, thus helping prevent structural failure.
- Support for Multiple Load Cases: Engineers can analyze different loading scenarios within a single model, making it easier to optimize designs for various conditions.
The Role of MONPNT1 in Solution 146
MONPNT1 is a specific output request used in conjunction with nastran solution 146 monpnt1 rms. It enables users to extract essential results at designated points within the structure, allowing for a more focused analysis of critical areas.
Types of Results Generated by MONPNT1
MONPNT1 generates several types of results, including:
- Nodal Displacements: The calculated movement of nodes in response to dynamic loads, which is crucial for understanding structural behavior.
- Velocities and Accelerations: Important for assessing the dynamic response of the structure and ensuring it operates within safe limits.
- Stress and Strain: Provides insights into the material behavior under dynamic conditions, essential for ensuring structural integrity.
RMS (Root Mean Square) Explained
In the context of Nastran, RMS (Root Mean Square) values are crucial for evaluating the dynamic responses of structures. RMS is a statistical measure that quantifies the magnitude of varying quantities, such as displacement or acceleration, over a given time period.
Importance of RMS in Dynamic Analysis
- Realistic Assessment: RMS values provide a more accurate representation of a structure’s response under dynamic loads, helping engineers to make informed decisions.
- Performance Evaluation: RMS calculations enable engineers to assess how well a structure performs under operational conditions, ensuring it meets safety standards.
- Comparative Analysis: By comparing RMS values across different scenarios, engineers can identify the most efficient design solutions.
How RMS Values Are Calculated in Nastran
In Nastran, RMS values are computed based on the time history of dynamic responses at specified points within the model. The process involves the following steps:
- Time History Data Collection: As the analysis runs, Nastran collects displacement, velocity, and acceleration data over time.
- RMS Calculation: The RMS values are calculated using the formula:RMS=1T∫0T(f(t))2dtRMS = \sqrt{\frac{1}{T} \int_0^T (f(t))^2 dt}RMS=T1∫0T(f(t))2dtwhere f(t)f(t)f(t) is the function of the variable of interest (e.g., displacement), and TTT is the total time period.
- Output Generation: The calculated RMS values are then presented in the analysis output, allowing engineers to review and interpret the results effectively.
Practical Applications of Nastran Solution 146 MONPNT1 RMS
Nastran Solution 146 MONPNT1 RMS has a wide array of applications across various engineering fields. Here are some notable examples:
1. Aerospace Engineering
In aerospace, ensuring the structural integrity of aircraft components under dynamic loads is paramount. Engineers utilize Solution 146 to analyze:
- Vibration Modes: Identifying the natural frequencies of aircraft components to prevent resonance during flight.
- Dynamic Loading Scenarios: Assessing how wings and fuselage sections respond to turbulence and other aerodynamic forces.
2. Automotive Engineering
In the automotive sector, vibration analysis is crucial for vehicle comfort and safety. nastran solution 146 monpnt1 rms is employed to evaluate:
- Suspension Systems: Analyzing how suspension components respond to road irregularities and ensuring they operate within safe limits.
- Body Structure: Evaluating how the vehicle body reacts to vibrations generated by the engine and road conditions.
3. Civil Engineering
In civil engineering, structures must withstand various dynamic loads, including seismic events. Solution 146 is applied to:
- Building Structures: Analyzing the natural frequencies of buildings to enhance their earthquake resilience.
- Bridges: Evaluating how bridge components respond to dynamic loads from traffic and environmental factors.
4. Manufacturing and Machinery
In manufacturing, machines often experience vibrations that can affect performance. Engineers use Nastran to:
- Optimize Machinery Design: Assessing how machine components react to operational vibrations to enhance durability and efficiency.
- Prevent Failures: Identifying potential failure points in machinery by analyzing dynamic responses.
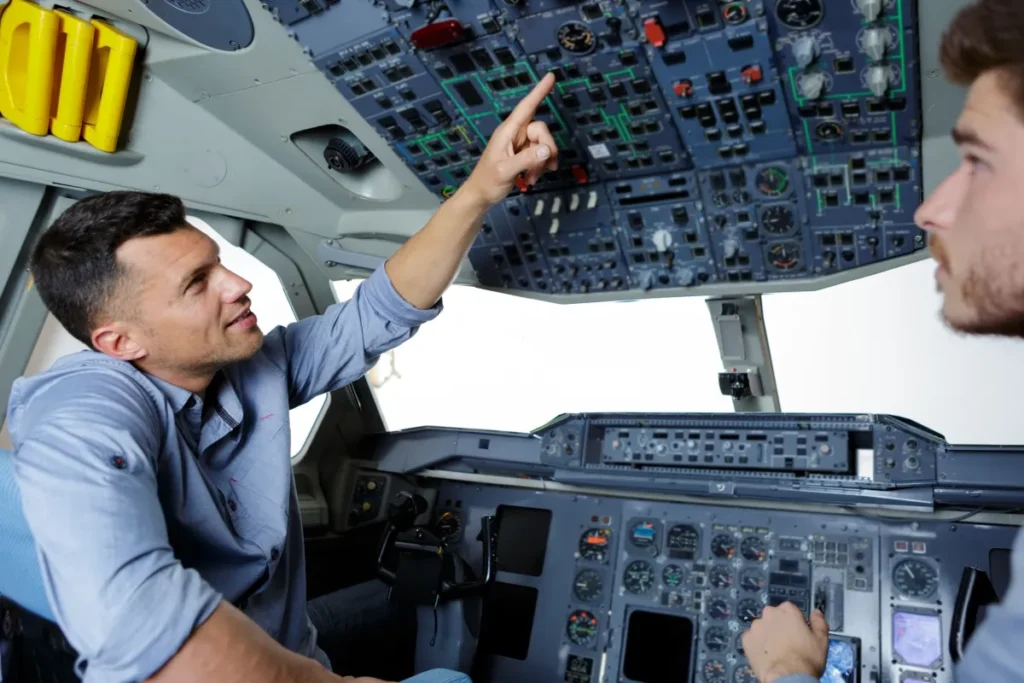
Best Practices for Using Nastran Solution 146 MONPNT1 RMS
To maximize the effectiveness of Nastran Solution 146 MONPNT1 RMS, engineers should consider the following best practices:
1. Proper Model Setup
A well-defined finite element model is essential for accurate results. Key considerations include:
- Mesh Quality: Ensure the mesh is refined enough to capture critical areas without being computationally excessive.
- Boundary Conditions: Define appropriate boundary conditions that mimic real-world constraints and loading scenarios.
2. Comprehensive Load Cases
Incorporate multiple load cases to evaluate various scenarios, including:
- Static Loads: Assessing how the structure behaves under constant loads.
- Dynamic Loads: Evaluating the effects of transient forces such as impacts or vibrations.
3. Sensitivity Analysis
Conducting a sensitivity analysis can help identify how changes in design parameters affect results(nastran solution 146 monpnt1 rms). This process involves:
- Varying Key Parameters: Adjusting material properties, boundary conditions, or geometry to evaluate their impact on RMS values.
- Interpreting Results: Analyzing how variations influence the dynamic response, leading to more robust design decisions.
4. Review and Validation of Results
Always review and validate results against experimental or analytical benchmarks to ensure accuracy. This involves:
- Cross-Referencing: Comparing Nastran results with previous studies or experiments.
- Peer Review: Engaging with colleagues to review methodologies and findings for potential improvements.
5. Continuous Learning
Stay updated with the latest advancements in Nastran and FEA methodologies. This can be achieved through:
- Training Programs: Participating in workshops and courses focused on Nastran.
- Community Engagement: Engaging with forums and user communities to exchange knowledge and experiences.
Conclusion
Nastran Solution 146 MONPNT1 RMS is an invaluable tool for engineers engaged in dynamic analysis, offering critical insights into the behavior of structures under varying loads. By leveraging its capabilities, engineers can design safer and more resilient structures across various industries, from aerospace to civil engineering.
Understanding the intricacies of MONPNT1 and the significance of RMS values enhances the ability to assess and optimize designs effectively. With best practices in mind, engineers can maximize the benefits of Nastran, contributing to advancements in engineering design and safety.
As industries continue to evolve and face new challenges, the role of tools like Nastran will be increasingly vital in shaping the future of engineering and design.